Kunde: Fruchtverarbeitendes Unternehmen
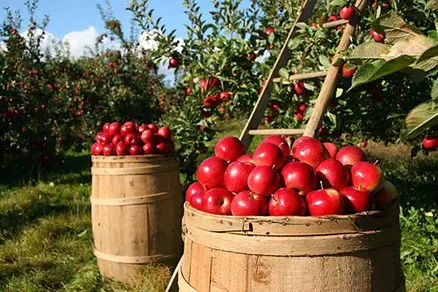
Fruchtaufstriche, Konfitüren, Dosenfrüchte und sogar Milcherzeugnisse gehören zum Produktportfolio eines der führenden europäischen Unternehmen zur Fruchtverarbeitung mit Standort in Mitteldeutschland. So hat sich der Standort mittlerweile vom kleinen Unternehmen mit regionaler Obstverarbeitung zum Marktführer in diesem Segment entwickelt. Eine zuverlässige Hygiene im Kühlturm und eine kontinuierliche Anlagenverfügbarkeit zur Aufrechterhaltung der Kühlprozesse sind daher für die Produktion von entscheidender Bedeutung.
Anforderung: Konstante Kühlwasserqualität für weniger Betriebsunterbrechungen
Jährlich durchlaufen vor Ort Millionen an Gläsern und Dosen zwei Linien, in denen die Fruchtprodukte pasteurisiert und damit haltbar gemacht werden. Dafür werden sie in einer Hitzezone mit ca. 90 Grad heißem Wasser berieselt und für rund zwanzig Minuten erhitzt. Daran schließt sich direkt eine Kühlzone an, in der die Konserven mit 30 Grad warmem Wasser wieder heruntergekühlt werden. So wird der Kochprozess abrupt gestoppt und damit auch die chemische Reaktion. Eine längere Hitzeeinwirkung würde zu Verfärbungen am Obst und auch zu Qualitätseinbußen führen. Letztlich sollen Geschmack und Nährstoffgehalt der Früchte weitestgehend erhalten bleiben, damit das Kundenerlebnis ungetrübt ist.
Das Management von Kühlwasser-Systemen umfasst zahlreiche Herausforderungen. Es drohen regelmäßig Verunreinigungen durch Feststoffe, Staub oder Pollen, die das bakterielle Wachstum fördern können. Biofilme entstehen, die zu gesundheitlichen Gefährdungen auswachsen können: Thema Legionellen. Darum muss die Qualität des Kühlwassers kontinuierlich kontrolliert und konditioniert werden, um Korrosion oder auch Kalkablagerungen zu verhindern.
Im Kühlkreislauf kam es immer wieder zu erheblichen Problemen, was regelmäßige Unterbrechungen zu Wartungszwecken zur Folge hatte. Während des Durchlaufs durch den Pasteur öffneten sich hin und wieder einzelne Gläser oder Dosen, so dass Obstprodukte und Fruchtreste in das Kühlwasser gelangten. Besonders im Sommer und in der Herbstzeit kam es durch diesen Fruchteintrag zu vermehrtem biologischem Wachstum im Kühlsystem, das dann – verbunden mit den entsprechenden Betriebsunterbrechungen – mühsam gereinigt werden musste. Daher fiel schon bald die Entscheidung, das Kühlsystem komplett neu aufzusetzen.
Lösung: Getrennte Kreisläufe, Kühlturmreinigung & smartes Kühlwasser-Management
Als erste Maßnahme wurde das bestehende gesamte Kühlsystem in zwei Kreisläufe aufgetrennt. Ein kleinerer geschlossener Kreislauf mit ca. 35 m3 Inhalt geht direkt in den Pasteur. Dieser ist über einen Plattenwärmetauscher mit einem größeren, insgesamt 50 m3 großen, offenen Sekundär-Kreislauf verbunden, der mit einer Kühlleistung von rund vier Megawatt das erwärmte Wasser rückkühlt.
Nach der Auftrennung der Kreisläufe führte Veolia Water Technologies eine professionelle Kühlturmreinigung mit Inspektion, Desinfektion und vorbeugender Instandhaltung durch. Durch diese Maßnahme konnte das Kühlsystem auf die neuen Anforderungen eingestellt werden und gleichzeitig die Vorgaben aus der 42. Bundesimmissionsschutzverordnung (42. BImSchV) problemlos einhalten.
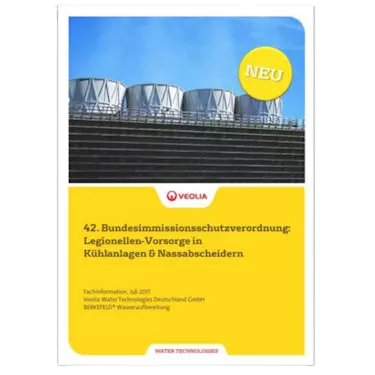
Die 42. BImSchV aus dem Jahr 2017 ist ebenso wie die VDI-Richtlinie 2047 maßgeblich für den hygienisch sicheren Betrieb von Verdunstungskühlanlagen. Mit den zum Teil strengen Vorschriften will der Gesetzgeber vor allem der Gefahr durch ein übermäßiges Wachstum von Legionellen vorbeugen. Denn immer wieder kommt es im Umkreis von Kühltürmen unterschiedlicher Branchen zu gesundheitlichen Schäden bei Mitarbeiter:innen oder auch Anwohnern, die durch verunreinigte Anlagen hervorgerufen werden. Durch die zuverlässige Überwachung und korrekte Dosierung der passenden Kühlwasser-Chemikalien lassen sich diese Gefahren beseitigen.
Kühlwasserqualität automatisiert regeln und aus der Ferne überwachen
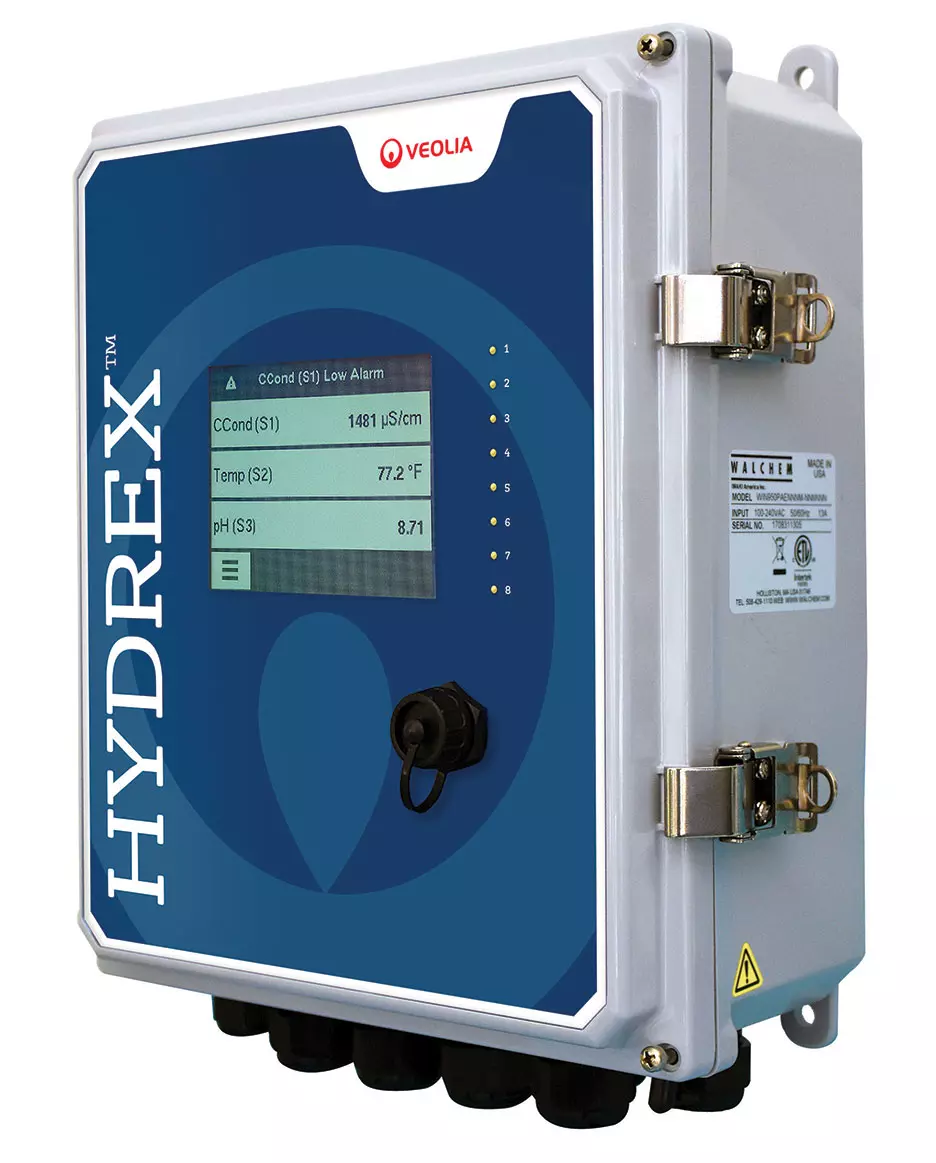
Um die Steuerung des Kühlsystems weitgehend zu automatisieren, wurde der neue Hydrex Controller CT in den großen Kühlkreislauf installiert. Der Controller dient als Mess- und Regelanlage für das Kühlwasser. Dabei handelt es sich um eine intelligente Multiparametereinheit, die kontinuierlich die relevanten Wasserwerte bestimmt und dokumentiert. Integrierte Sensoren ermitteln die Redox-Spannung, den Leit- und pH-Wert und die Produktkonzentration. Schwanken diese Werte kurzfristig, geben sie damit einen Hinweis auf tiefer gehende Ursachen, die umgehend behoben werden müssen. Bei Bedarf steuert der Hydrex Controller CT bis zu vier Dosierpumpen für die Chemikalienzugabe an und reagiert direkt auf entsprechende Abweichungen. Das Gerät sorgt so automatisch für die Einhaltung der voreingestellten Wasserparameter.
Der Hydrex Controller wurde an die Online-Service-Plattform Hubgrade angebunden. Der Einbau des Controllers ermöglicht nun die Visualisierung der Anlagenwerte jederzeit an jedem Arbeitsplatz und sogar von unterwegs aus.